Plastic extrusion for intricate profiles and custom designs
Plastic extrusion for intricate profiles and custom designs
Blog Article
A Comprehensive Guide to the Refine and Advantages of Plastic Extrusion
In the large world of manufacturing, plastic extrusion emerges as a extremely effective and crucial process. Altering raw plastic into constant profiles, it satisfies a huge selection of industries with its impressive flexibility. This guide intends to elucidate the elaborate actions involved in this technique, the types of plastic proper for extrusion, and the game-changing benefits it offers the market. The occurring conversation guarantees to unfold the real-world impacts of this transformative process.
Recognizing the Fundamentals of Plastic Extrusion
While it may show up complicated at first look, the process of plastic extrusion is basically easy. The procedure begins with the feeding of plastic product, in the type of pellets, granules, or powders, right into a heated barrel. The designed plastic is after that cooled down, solidified, and reduced right into desired lengths, completing the process.
The Technical Refine of Plastic Extrusion Explained
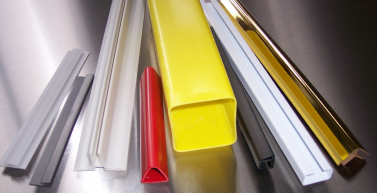
Kinds Of Plastic Suitable for Extrusion
The selection of the appropriate sort of plastic is a critical aspect of the extrusion procedure. Numerous plastics offer unique residential properties, making them a lot more matched to specific applications. Polyethylene, as an example, is commonly utilized due to its inexpensive and simple formability. It offers superb resistance to chemicals and dampness, making it suitable for products like tubes and containers. Polypropylene is one more preferred selection due to its high melting point and resistance to exhaustion. For more durable applications, polystyrene and PVC (polyvinyl chloride) are typically selected for their toughness and toughness. These are common alternatives, the choice ultimately depends on the details demands of the product being created. Recognizing these plastic types can considerably boost the extrusion process.
Contrasting Plastic Extrusion to Various Other Plastic Forming Methods
Understanding the sorts of plastic ideal for extrusion leads the method for a broader discussion on exactly how plastic extrusion piles up versus other plastic forming methods. These consist of shot molding, strike molding, and thermoforming. Each method has its unique uses and benefits. Shot molding, as an example, is outstanding for producing detailed components, while impact molding is perfect for hollow items like bottles. Thermoforming excels at creating superficial or big parts. Nonetheless, plastic extrusion is unrivaled when it comes to creating constant accounts, such as seals, gaskets, and pipelines. It additionally allows for a consistent cross-section along the length of the product. Hence, the choice of approach mostly depends on the end-product needs and see this specifications.
Key Benefits of Plastic Extrusion in Production
In the world of production, plastic extrusion provides lots of considerable advantages. One noteworthy benefit is the cost-effectiveness of the process, that makes it an economically attractive production technique. Additionally, this method offers remarkable product flexibility and improved manufacturing speed, therefore boosting general manufacturing effectiveness.
Cost-Effective Manufacturing Technique
Plastic extrusion jumps to the forefront as a cost-efficient production approach in manufacturing. Additionally, plastic extrusion requires much less power than traditional production methods, adding to lower functional costs. Generally, the financial advantages make plastic extrusion a very eye-catching alternative in the production industry.

Superior Item Adaptability
Beyond the cost-effectiveness of plastic extrusion, another significant benefit in making hinge on its remarkable product flexibility. This procedure enables for the creation of a large variety of products with differing forms, dimensions, and layouts, from basic plastic sheets to elaborate accounts. The versatility is connected to the extrusion pass away, which can be tailored to generate the wanted item style. This makes plastic extrusion an excellent option for sectors that call for personalized plastic elements, such as auto, get more building, and packaging. The capacity to produce diverse products is not only advantageous in conference details market demands however additionally in allowing suppliers to check out new product with marginal capital expense. Essentially, plastic extrusion's product flexibility fosters advancement while boosting functional efficiency.
Enhanced Production Speed
A considerable benefit of plastic extrusion lies in its enhanced manufacturing speed. Couple of other production procedures can match the speed of plastic extrusion. Furthermore, the capability to preserve regular high-speed manufacturing without giving up item quality sets plastic extrusion apart from various other methods.
Real-world Applications and Effects of Plastic Extrusion
In the world of production, the technique of plastic extrusion holds profound significance. The economic advantage of plastic extrusion, mainly its high-volume and economical output, has revolutionized production. The sector is constantly making every effort for technologies in eco-friendly and recyclable materials, indicating a future where the benefits of plastic extrusion can be kept without jeopardizing environmental sustainability.
Final thought
Finally, plastic extrusion is a effective and very reliable approach of changing resources into diverse items. It supplies countless benefits over internet various other plastic creating approaches, consisting of cost-effectiveness, high output, very little waste, and layout flexibility. Its effect is profoundly felt in different sectors such as construction, automobile, and consumer goods, making it a crucial procedure in today's production landscape.
Digging much deeper right into the technical process of plastic extrusion, it starts with the choice of the suitable plastic material. When cooled, the plastic is reduced into the required sizes or wound onto reels if the product is a plastic film or sheet - plastic extrusion. Contrasting Plastic Extrusion to Other Plastic Forming Techniques
Recognizing the kinds of plastic ideal for extrusion leads the means for a more comprehensive discussion on how plastic extrusion piles up against various other plastic developing methods. Couple of various other manufacturing procedures can match the rate of plastic extrusion.
Report this page